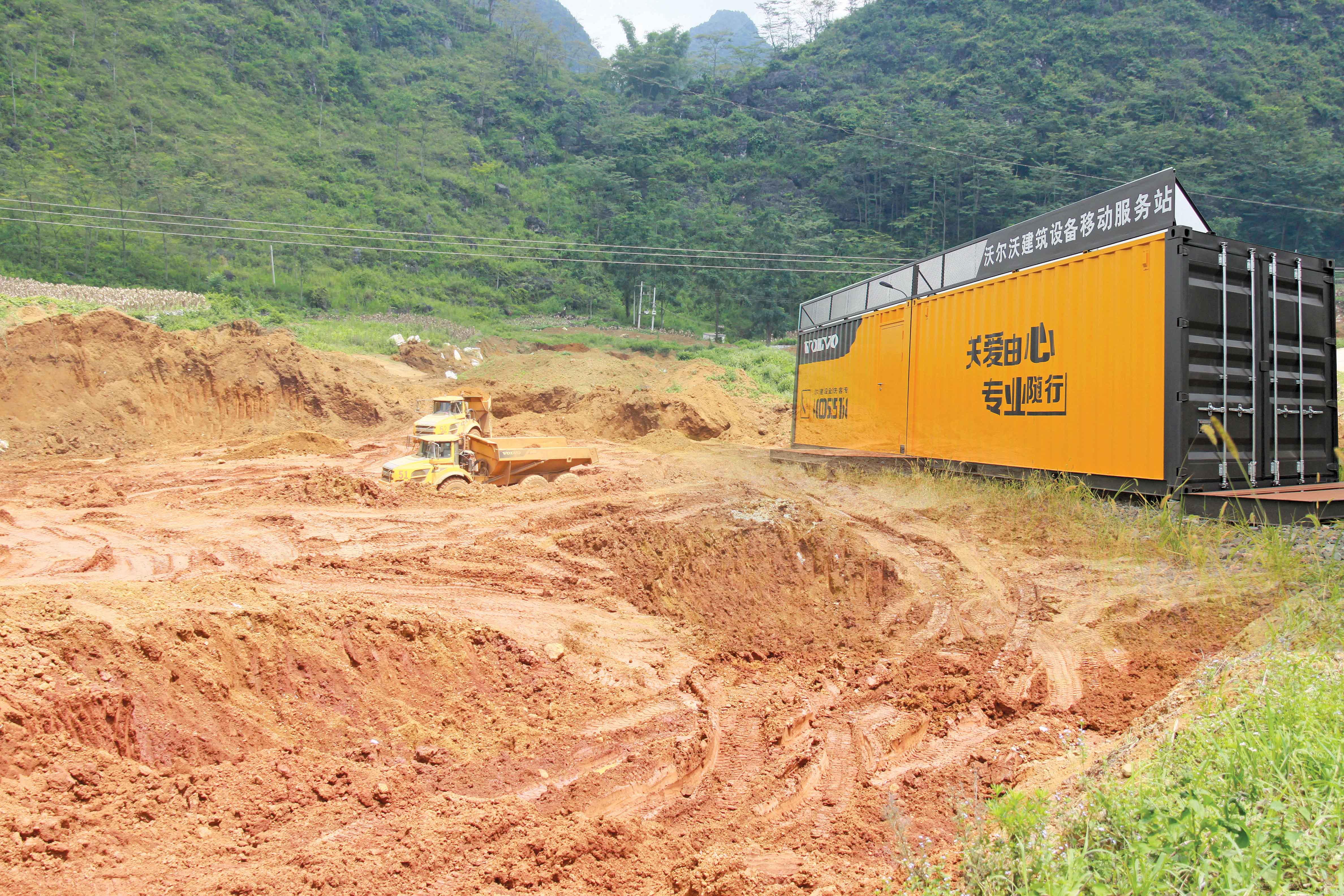
The parts storage system has cut downtime for the producer
This system is now being used at the Guangxi Pingguo Aluminium Company, a major aluminium ore mining company.
Currently operating 64 Volvo articulated haulers, eight crawler excavators and eight wheeled loaders, GPAC is faced with the fleet maintenance challenge of ensuring machine availability in tough conditions, without losing productivity.
The producer approached dealer
Delays resulted in financial loss for the company. But with parts stored in the container near the job site, the mobile service station means Volvo Construction Equipment can provide a 24-hour on-site service and parts supply.
In addition to cutting ownership costs, the initiative is environmentally friendly and is easily installed at the start of a project, then removed upon completion. Proving popular with customers, the innovative yellow box is being rolled out across the country, in demand at remote mines and work sites to provide customers with full service and parts in the shortest possible time.