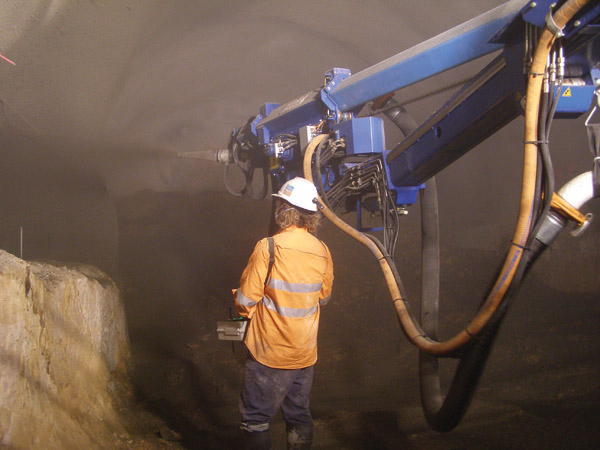
New spraying technology from BASF is offering advances in tunnelling sealing performance
New tunnelling technology from BASF has helped cut construction time on a major tunnel project in Australia.
The system has been used to speed waterproofing, an important point as the link runs underneath one of Australia's major rivers. The spray-applied polymer membrane provided by aThe 4.8km tunnel was completed seven months ahead of schedule and at its lowest point Clem 7 runs some 70m below sea level. While the original specification of a traditional sheet membrane system was initially used, the installation of the sheet system proved time-consuming.
A membrane system with a fast rate of application was required because the delays were hampering the fast-track construction program.
The project's engineers needed to find a replacement waterproofing solution that was quick and easy to apply. The solution was a sprayapplied polymer membrane from BASF Construction Chemicals, MASTERSEAL 345. Once trained in the application of the product, it was possible for the LBBJV crew to apply up to 2,000m²/day of membrane. The product was applied with one of BASF's
MASTERSEAL 345 is a singlecomponent spray-applied powder product, which bonds layers of sprayed or cast concrete. When mixed with water at the nozzle and delivered to the substrate via compressed air, it provides a tough, elastic membrane layer. The flowable nature of the freshly applied product ensures all irregularities in the porous profile of the tunnel wall are coated evenly, providing a positive waterproof seal.
Over 68,000m² of the product was applied in various sections of the project, supplying the contractor with the quickly applied, high quality waterproofing option required.
Clem 7 comprises twin road tunnels, excavated using two 12.4m diameter TBMs and 10 roadheaders, to link the Brisbane suburbs of Woolloongabba in the south to Bowen Hills in the north. Extensive surface works were required to tie the tunnels into the existing road network at six portal locations. The tunnel was designed to ease inner-city congestion.