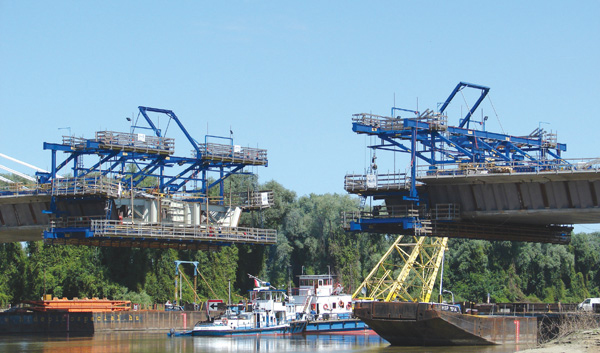
Two pairs of the new Doka cantilever forming traveler are in service on the Tisza Bridge
The Hungarian government has been investing heavily in extending and improving the country's motorway and trunk road network.
One such project is the M43 motorway, currently being built to link Szeged and Makó in south-eastern Hungary. The 32km long route branches off the M5/E75 Budapest (Hungary) to Belgrade (Serbia) motorway at Szeged, and is part of Pan-European Corridor IV to Bucharest (Romania).
With its composite steel segment plus cast-in-place concrete (CIPC) superstructure and its width of 30m the 372m long motorway bridge crossing the River Tisza just outside Szeged makes some tough demands of the contractors.
To tackle this challenging bridge project, the Hungarian construction company Hídépítö is "relying on the high capability of the203 Doka cantilever forming traveller (CFT), and benefiting from the smooth construction progress that this makes possible." The constructional design of the new bridge takes the principle of the extradosed bridge as its starting point, and combines this with the advantages of a steel-concrete composite bridge.
The superstructure is being built as a triple-cell cross section with truss-like steel segments and a CIP deck
slab and base slab. The comparatively low weight of this design, and the combination of integral and external pre-stressing by means of cable-stays, allow for a slender deck cross section and relatively low bridge pylons. It is the first time that this method has been used in Hungary.
"To ensure a smooth construction workflow and not take any risks, we decided to go for a highly efficient all-in-one solution comprising the Doka cantilever forming traveller and Doka formwork. The strong technical support was another key factor behind this decision," explains Hídépítö's technical manager János Barta.
Due to the large cross sectional width of 30m, on this project the rentable Doka cantilever forming travellers are designed with four rather than the usual two longitudinal trusses.
High-capacity drive components mean that the CFTs can still be travelled to the next concrete casting section, without difficulty, on the two outside longitudinal trusses. This means that considerably less equipment is needed and repositioning takes place quickly and easily, says Doka.
The company says that the method for constructing the 5m long casting-sections is very different from that used in conventional balanced-cantilever bridge building projects.
Once the CFT has been precisely set up and aligned, the 28tonne steel segments, together with the rebar for the base slab, are hoisted into place from the river by a floating crane. They are then positioned on the bottom grid of the CFT and aligned with the aid of hydraulic cylinders. Next, the steel segments are welded to the existing structure, and the cantilever arm formwork is then pressed up against them, and the base slab is poured.
To enable the floating crane to hoist the steel segments into place without difficulty, regardless of the level of the river, the cross girder on the narrow side has a rear-inclined portal.
"This custom-construction makes it possible for our crane operator to place the steel segments onto the bottom grid very precisely, without grazing the CFT, even when conditions get difficult," explains János Barta, technical manager at Hídépítö.
Once the base slab has been completed, the formwork for the deck slab is moved forward from the most recently cast section. Owing to the limited space available between the steel segments, site management opted for the easy-to-reposition Dokaflex slab formwork and the Staxo 100 load-bearing tower system. Following the set-up operations on the cantilever arm formwork, the deck slab is cast in a single pour. In this sequence, a casting section is completed every eleven days.
"With the Doka CFTS, you can be sure of getting a regular workflow in every phase of the construction operations," says Barta.
As well as the two pairs of CFTs, Doka also planned and is supplying the formwork for the two massive pier heads, and a climbing formwork solution for both of the 22m tall bridge pylons.
One such project is the M43 motorway, currently being built to link Szeged and Makó in south-eastern Hungary. The 32km long route branches off the M5/E75 Budapest (Hungary) to Belgrade (Serbia) motorway at Szeged, and is part of Pan-European Corridor IV to Bucharest (Romania).
With its composite steel segment plus cast-in-place concrete (CIPC) superstructure and its width of 30m the 372m long motorway bridge crossing the River Tisza just outside Szeged makes some tough demands of the contractors.
To tackle this challenging bridge project, the Hungarian construction company Hídépítö is "relying on the high capability of the
The superstructure is being built as a triple-cell cross section with truss-like steel segments and a CIP deck
slab and base slab. The comparatively low weight of this design, and the combination of integral and external pre-stressing by means of cable-stays, allow for a slender deck cross section and relatively low bridge pylons. It is the first time that this method has been used in Hungary.
"To ensure a smooth construction workflow and not take any risks, we decided to go for a highly efficient all-in-one solution comprising the Doka cantilever forming traveller and Doka formwork. The strong technical support was another key factor behind this decision," explains Hídépítö's technical manager János Barta.
Due to the large cross sectional width of 30m, on this project the rentable Doka cantilever forming travellers are designed with four rather than the usual two longitudinal trusses.
High-capacity drive components mean that the CFTs can still be travelled to the next concrete casting section, without difficulty, on the two outside longitudinal trusses. This means that considerably less equipment is needed and repositioning takes place quickly and easily, says Doka.
The company says that the method for constructing the 5m long casting-sections is very different from that used in conventional balanced-cantilever bridge building projects.
Once the CFT has been precisely set up and aligned, the 28tonne steel segments, together with the rebar for the base slab, are hoisted into place from the river by a floating crane. They are then positioned on the bottom grid of the CFT and aligned with the aid of hydraulic cylinders. Next, the steel segments are welded to the existing structure, and the cantilever arm formwork is then pressed up against them, and the base slab is poured.
To enable the floating crane to hoist the steel segments into place without difficulty, regardless of the level of the river, the cross girder on the narrow side has a rear-inclined portal.
"This custom-construction makes it possible for our crane operator to place the steel segments onto the bottom grid very precisely, without grazing the CFT, even when conditions get difficult," explains János Barta, technical manager at Hídépítö.
Once the base slab has been completed, the formwork for the deck slab is moved forward from the most recently cast section. Owing to the limited space available between the steel segments, site management opted for the easy-to-reposition Dokaflex slab formwork and the Staxo 100 load-bearing tower system. Following the set-up operations on the cantilever arm formwork, the deck slab is cast in a single pour. In this sequence, a casting section is completed every eleven days.
"With the Doka CFTS, you can be sure of getting a regular workflow in every phase of the construction operations," says Barta.
As well as the two pairs of CFTs, Doka also planned and is supplying the formwork for the two massive pier heads, and a climbing formwork solution for both of the 22m tall bridge pylons.