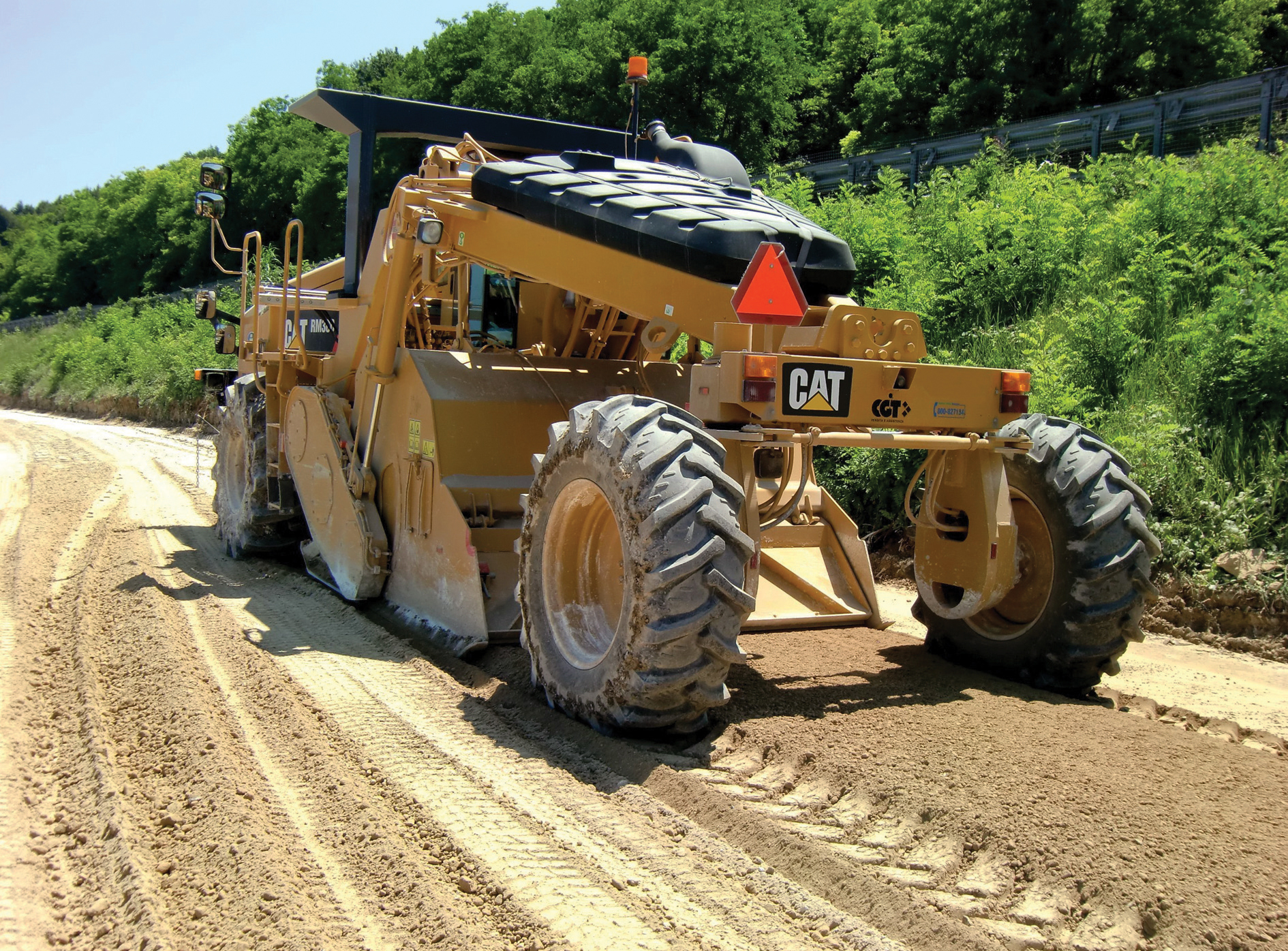
The Caterpillar RM300s had to work close to the existing route
The use of recycling and stabilisation equipment has played a key role in adding new lanes to a congested Italian highway. Running from Bologna to Taranto, the A14 Autostrade has seen a major increase in traffic volumes for several years. Data shows that traffic has increased around 4% year on year with some 110,000 vehicles using the highway/day. The traffic growth trend looks set to continue and this resulted in the Italian Government opting to upgrade and widen the route.
The multi-phased project took place along a 154.7km section between Rimini North and a future junction at Porto Sant’Elpidio. The project widened the road from two to three lanes with the addition of an emergency lane. In addition 10 existing junctions were upgraded and five new junctions built. They are located in Pesaro South, Fano North, Marina di Monte Marciano, Ancona West and Port Sant’Elpidio.
Contractor Ghea Sistem handled most of the challenging soil stabilisation work required and has completed the Northern part of Section 2 of the project; a 28km stretch from Cattolica to Pesaro. Because of the clay-based soil and of the high water table, the section required extensive work to raise the level of the road. “The main challenges include the proximity of the water table which is almost at ground level in places,” said Alessio Cagnola, who owns Ghea Sistem with his brother, Paolo.
The firm said that as 95% of the work was carried out alongside the existing route, this created issues with space, and sometimes large quantities of soil close to the traffic needed to be excavated to widen the road and to allow the construction of retaining walls. It could have interfered with the placement of concrete structures, such as large pipe and box culverts.
Tasks included grading slopes, and the saturated soil was unstable for the work crews at times because of heavy rain. On the more even grades, sometimes the soil was too saturated to be moved or for equipment to operate. Ghea used two methods to stabilise the road and the wide even stretches of road were stabilised with a178 Caterpillar RM300. In poor soil conditions, lime additives were sprayed on the soil and mixed by the RM300.
Ghea Sistem excavated clay-based soil to make room for culverts and other infrastructure and had to deal with pockets of unstable gumbo and saturated sub-soil. The challenge of establishing the load bearing capacity was further compounded by the forces of nature and the instability of the remaining sub-surface soil. Temporary soil stabilisation sites were established and trucks transported material to each site. Non-usable soil was separated and blended into the surrounding terrain. The RM300 was used to blend lime additives into the soil that was suitable for re-use and this was hauled back for use as fill to build the new lane. The grade had to be raised from 2-5m where the road crossed the high water table and areas of marginal soil consistency.
A base layer of graded aggregate hauled in from a nearby quarry and in addition to the reclaimed fill, suitable soil was excavated from high-ground pits. Soil topped with a lime additive was used to raise the grade to the required height. Project specifications called for 20% of lime blended into each stabilised layer. Three Cat RM300 passes were applied to each layer of the stratified soil-lime mix to achieve the target composition. A grader ensured each load was placed at the correct depth and a soil compactor completed the third step. This three-step sequence was followed to establish each soil/lime layer and the Cat RM300 played a key role to help achieve a stable base. Depending on the time of year and on the soil moisture content, the soil was watered between the first and second passes of the Cat RM300. This ensured that the lime was properly hydrated to achieve the best mix in preparation for the compacting finish.
The material left behind was consistent in size, with no large chunks or clumps of clay, while its colour was uniform indicating that the additives and clay-based soil had been thoroughly mixed.
The multi-phased project took place along a 154.7km section between Rimini North and a future junction at Porto Sant’Elpidio. The project widened the road from two to three lanes with the addition of an emergency lane. In addition 10 existing junctions were upgraded and five new junctions built. They are located in Pesaro South, Fano North, Marina di Monte Marciano, Ancona West and Port Sant’Elpidio.
Contractor Ghea Sistem handled most of the challenging soil stabilisation work required and has completed the Northern part of Section 2 of the project; a 28km stretch from Cattolica to Pesaro. Because of the clay-based soil and of the high water table, the section required extensive work to raise the level of the road. “The main challenges include the proximity of the water table which is almost at ground level in places,” said Alessio Cagnola, who owns Ghea Sistem with his brother, Paolo.
The firm said that as 95% of the work was carried out alongside the existing route, this created issues with space, and sometimes large quantities of soil close to the traffic needed to be excavated to widen the road and to allow the construction of retaining walls. It could have interfered with the placement of concrete structures, such as large pipe and box culverts.
Tasks included grading slopes, and the saturated soil was unstable for the work crews at times because of heavy rain. On the more even grades, sometimes the soil was too saturated to be moved or for equipment to operate. Ghea used two methods to stabilise the road and the wide even stretches of road were stabilised with a
Ghea Sistem excavated clay-based soil to make room for culverts and other infrastructure and had to deal with pockets of unstable gumbo and saturated sub-soil. The challenge of establishing the load bearing capacity was further compounded by the forces of nature and the instability of the remaining sub-surface soil. Temporary soil stabilisation sites were established and trucks transported material to each site. Non-usable soil was separated and blended into the surrounding terrain. The RM300 was used to blend lime additives into the soil that was suitable for re-use and this was hauled back for use as fill to build the new lane. The grade had to be raised from 2-5m where the road crossed the high water table and areas of marginal soil consistency.
A base layer of graded aggregate hauled in from a nearby quarry and in addition to the reclaimed fill, suitable soil was excavated from high-ground pits. Soil topped with a lime additive was used to raise the grade to the required height. Project specifications called for 20% of lime blended into each stabilised layer. Three Cat RM300 passes were applied to each layer of the stratified soil-lime mix to achieve the target composition. A grader ensured each load was placed at the correct depth and a soil compactor completed the third step. This three-step sequence was followed to establish each soil/lime layer and the Cat RM300 played a key role to help achieve a stable base. Depending on the time of year and on the soil moisture content, the soil was watered between the first and second passes of the Cat RM300. This ensured that the lime was properly hydrated to achieve the best mix in preparation for the compacting finish.
The material left behind was consistent in size, with no large chunks or clumps of clay, while its colour was uniform indicating that the additives and clay-based soil had been thoroughly mixed.