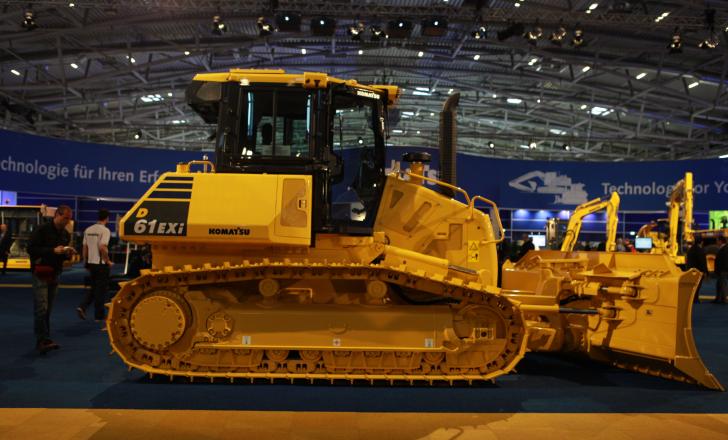
Komatsu has introduced Intelligent machines
It has started the roll-out of its intelligent machines with the D61EXi/PXi-23 dozer and a prototype PC210LCi-10 excavator.
The Japanese manufacturer has teamed up with
On the dozer, the system not only senses the machine’s position and cuts to grade, it also detects the load on the blade and will automatically reduce the cut to prevent track slip.
In integrating the system as a factory fit, all instrumentation has been removed from the blade with the antenna relocated to the top of the cab for improved protection and accuracy, while stroke-sensing cylinders are used to determine the blade’s position.
The system can be used for all types of dozing work, be it rough cutting or finishing, as it automatically switches between the two modes as the cut approaches grade.
The operator has the choice of four dozing modes and three load settings and, during operation, the blade lowers until it meets the target surface or until the blade load reaches a maximum. Before the blade overloads, it is automatically lifted slightly to minimise track slip and maintain forward momentum.
According to Komatsu, this maximises productivity, minimises track wear and allows novice operators to work as productively as the most skilled.
With the PC210LCi excavator, the operator digs as normal without looking at the monitor for grade information. The instrumented machine will not cut below the programmed grade. This reduces the time needed for finishing flat bottom trenches, grading batters and the like without slowing the any preliminary excavations.
According to Komatsu president and CEO Tetsuji Ohashi, productivity gains with intelligent machines could be in the region of 40%, depending on the operation, and payback of the on-cost should be achieved within a year.
He sees a combination of time and cost savings, and the shortage of skilled operators leading to increased uptake in the use of such systems, which will lead to a reduction in the price premium to a point where such systems will be standard fitment within the next 10 years.
Stand: B5.104/304
View more videosView more stories