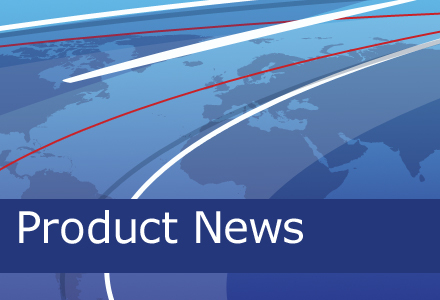
New ownership offers greater overseas potential for Barrier Systems
The first Barrier Systems machine in the UK is now operating on the M25 and a second unit is to be used on the M20 motorway to allow trucks to queue on the motorway. Leading to the Channel port of Dover the M20 carries heavy freight traffic in both directions and poor weather can disrupt ferry operation, leading to build-ups of trucks and the need for this novel queuing system. Meanwhile, with sister company
JD Sobol is vice president of sales and marketing at Barrier Systems and believes that there is a huge and untapped market for the firm's distinctive moveable worksite barrier concept in developing countries, as well as in the developed nations of North America or Western Europe. He said that there is minimal protection afforded highway construction workers in many developing countries but that the moveable barrier will help improve safety and reduce fatality rates.
The acquisition of Barrier Systems by steel component specialist Lindsay Manufacturing and the subsequent addition of Italian barrier firm Snoline to the group have brought economies of scale for the company as a whole. According to Jeff Shewmaker, Barrier Systems' marketing manager, his company is already co-operating with Snoline on new product development. He said that this is important as the two are also able to use their experience in their respective home markets to ensure any new products more accurately meet both customer needs and local regulations.
Sobol explained that Lindsay Manufacturing bought Barrier Systems and Snoline because it saw the huge growth potential for these businesses, given the need for infrastructure investment worldwide. Lindsay manufacturing supplies equipment for the water industry and saw this as a low growth sector. As the company is a supplier of sub-components to Barrier Systems, Lindsay manufacturing knew the business well and realised that infrastructure offered major growth potential, which was why it bought Barrier Systems, followed by Snoline. For Barrier Systems and Snoline, the purchase means that they will have a stronger supply of components and will be able to benefit from cost reductions through placing large batch orders across the group.
Lindsay Manufacturing has factories in Brazil and South Africa and is investigating the possibility of establishing a plant in Asia. This strong international spread will allow Barrier Systems to tackle a wider array of markets and also manufacture locally in countries such as Brazil, avoiding the issue of import costs. The Latin American highway sector is growing and provides many opportunities for Barrier Systems and Sobol said, "That will help us sell more products in the long term down there." The additional manufacturing capacity is important for Barrier Systems, which has seen demand increase rapidly and the company is already setting up new facilities in California to cope.
Quality of manufacture is important to the company and the mould units used to form the barrier sections are built to precise specifications, as well as being extremely durable. Sobol said, "They last forever." The moulds have to be made to a high standard to ensure a high degree of accuracy and precise location of components between sections. Chris Sanders is vice president and COO of Barrier Systems and said, "There's a lot of money in the tooling to make these barrier moulds." The moulds are purposely designed to be used by the customer close to the working area and Sanders said, "We make the barriers there as we don't want to have to ship the concrete sections." Each section weighs 635kg apiece, which makes it easy to appreciate why local manufacturing of the units is important. The weight of the units is important to the performance of the entire barrier in a working environment as this helps the barrier to retain its layout in the event of a vehicle collision. Performance is further improved due to the innovative tensioning system installed in the joints linking the sections together. Sanders said, "Everything is metal to metal, which is why it stays in line." He added that the sections are standardised and are effectively the same for all markets worldwide, as this reduces manufacturing costs and the price for the customer. "We developed one product for the US and European market," he said