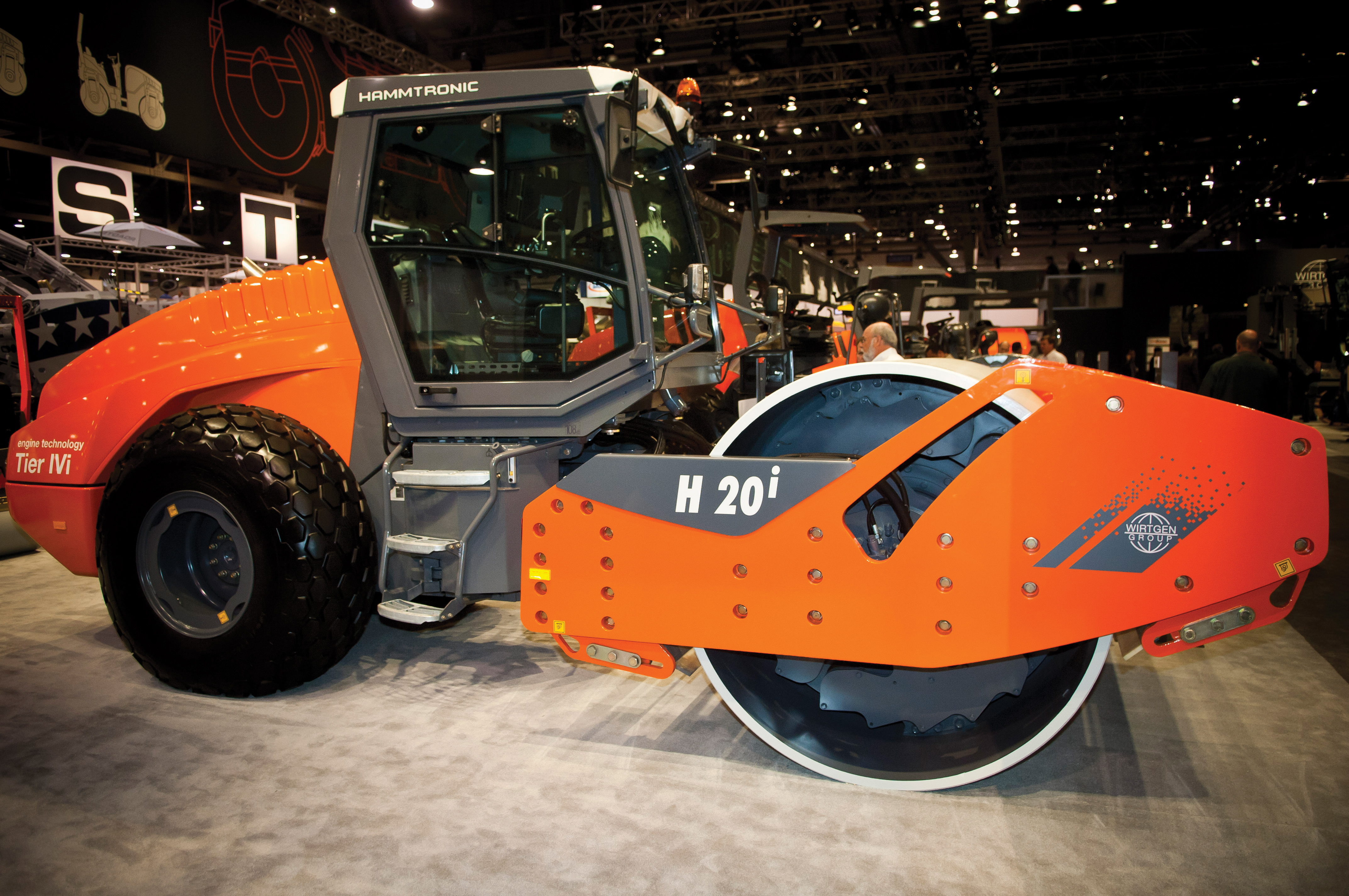
The new H20i soil compactor from HAMM shows how emissions performance can be achieved while retaining rearward visibility
Major advances are coming to soil compactors - Mike Woof reports
The unveiling ofIn the 1990s,
However, when the Tier 4 Interim and Tier 4 Final requirements were announced, there was widespread concern in the construction sector as to how these regulations would be met and the implications they would have for machines.
There was particular comment over how operator visibility improvements made over the years could be retained, given the need to fit bulky exhaust after-treatment equipment, as well as the extra cooling systems required. As Tier 4 Interim and Tier 4 Final engines run hotter than earlier generation diesels, they require more cooling as well as larger fans and radiators. But at the same time, the regulations have called for quieter operation and this has posed a challenge given that cooling fans are significant noise generators.
The unveiling of the HAMM H20i shows that the necessary rearward visibility can be retained, while meeting the necessary emissions targets and installing a Tier 4 Interim/Stage IIIB compliant engine. HAMM claims that its H20i is setting a lead in the industry by meeting the emissions requirements while offering plenty of power in reserve for compaction, even in tough operating conditions.
A key factor in the H20i being able to meet the requirements is its use of the compact Deutz diesel, while the machine's radiator is also sloped so as to lower its profile. To further ensure the operator visibility is good, the H20i has an unobstructed field of view from the large cab, due to the use of large glass panes in the windows. ...
The six cylinder
Running costs have also been addressed and the H20i is also said to be economical to run as it can be operated either in normal or ECO mode, to minimise fuel consumption.
Although the unit at the exhibition was a preproduction machine, it has been sold to a customer and the firm said that full production is due to start later this year. The 20tonne H20i will be followed into production by two further models in this line-up and these will share a similar design. The H18i will weigh some 18.3tonnes, while the larger H25i will weigh close to 25tonnes. When the two other machines are introduced, HAMM says that they will share many components and features of the mid-sized H20i, which has a 2.14m wide drum and is designed to deliver centrifugal forces of 331kN.
In other respects the H20i is a conventional soil compactor however and features the latest technology being installed on these machines by the leading manufacturers. For example, it is equipped with sensors so that the operator can monitor compaction and ensure that operations are carried out to required specifications.
While in the early 1990s, Ammann was a leader with its high visibility soil compactors, HAMM has now made its mark on this segment.
However the major rivals such as Ammann, BOMAG, Caterpillar and Volvo will not be willing to let HAMM steal a lead in this important market segment.